Understanding BGA Packages: An In-Depth Exploration
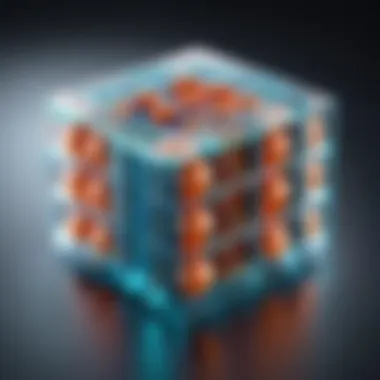
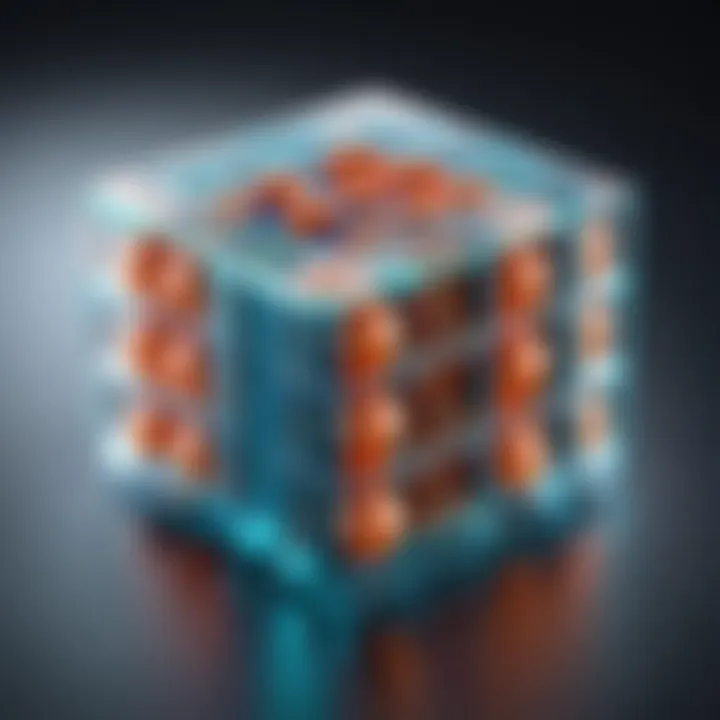
Intro
In the world of electronics, Ball Grid Array (BGA) packages are a crucial component of modern circuit board designs. Understanding these packages is essential for IT professionals and tech enthusiasts who aim to grasp the nuances of electronic packaging. BGA packages have gained traction due to their superior performance and space efficiency when compared to traditional packaging options.
This article delves into various dimensions of BGA technology, providing insights into their design, function, and application. By highlighting the advantages and disadvantages associated with BGA packaging, we aim to equip the reader with a profound knowledge that will aid in selecting and implementing these packages effectively.
The discussion also addresses manufacturing processes, industry standards, and critical considerations necessary for successful BGA integration. Additionally, we will explore current market trends influencing the BGA landscape, offering foresight into future innovations. Understanding these elements will not only enhance technical competency but will also facilitate informed decision-making in electronics design and production.
Hardware Overview
BGA packages are defined by their unique hardware attributes, which distinguish them from other packaging technologies. They provide a robust solution for high-density applications where space is at a premium.
Specifications
BGA packages vary widely in specifications depending on their intended application. Common artifacts include:
- Pitch Size: The distance between the centers of two adjacent solder balls, typically ranging from 0.5 mm to 1.0 mm.
- Size: BGA packages can range significantly in size, catering to various circuit designs. Smaller packages are ideal for compact devices, while larger ones accommodate more complex circuits.
- Ball Count: The number of solder balls can differ, influencing signal integrity and connectivity options. High pin count facilitates higher functionality in a limited area.
Performance Metrics
To evaluate the effectiveness of BGA packages, several performance metrics are taken into consideration:
- Thermal Conductivity: BGA packages operate efficiently at a broad range of temperatures, but their design must consider heat dissipation to prevent overheating.
- Electrical Performance: Metrics such as signal delay and crosstalk are critical to maintaining signal integrity. BGA technology often outperforms traditional designs in these areas.
Performance in these dimensions illustrates why BGA packages are increasingly preferred in high-performance electronics.
Software Analysis
Although BGA packages are predominantly hardware focused, the integration of software aspects cannot be overlooked. The interaction between software and hardware directly affects the functionality of BGA technology.
Features and Functionality
BGA packages come equipped with various features that enhance their usability, including:
- Automated Placement: Many BGA packages are designed for automated installation, reducing human error and increasing production efficiency.
- Improved Signal Routing: Advanced designs allow for better signal pathways, thus enhancing overall performance.
User Interface and Experience
The user interface associated with designing BGA packages can vary. Design software tools like Altium Designer or Cadence provide platforms that enable professionals to create optimized BGA layouts. The effectiveness of these tools is critical for ensuring that the electrical and thermal characteristics are accurately modeled throughout the development process.
BGA technology represents a shift towards higher efficiency in electronic packaging. Understanding its intricacies is vital for anyone involved in the electronics field.
Prologue to BGA Packages
Ball Grid Array (BGA) packages have become essential components in modern electronic devices. They provide a way to connect integrated circuits (ICs) to printed circuit boards (PCBs) using an array of solder balls. This technology stands out for its capacity to enable a higher density of connections and effective electrical performance.
The significance of BGA packages extends beyond their compact design. They effectively address the need for improved thermal performance, which is increasingly important in today’s miniaturized electronic systems. By dissipating heat more efficiently, BGAs help maintain operational reliability—something crucial for both consumer electronics and industrial applications.
In this article, we will explore several critical aspects of BGA technology:
- Design Features: Understanding grid arrangements and package sizes that contribute to performance.
- Electrical Performance: Analyzing how BGAs enhance signal integrity and impedance control.
- Advantages and Disadvantages: Weighing the benefits like higher pin density against challenges like inspection difficulties.
The relevance of studying BGA packages lies not only in their widespread use but also in their adaptability to various technological advancements. As we proceed, we will uncover how these packages fit into larger industry trends and how understanding their intricacies can benefit technology professionals and enthusiasts alike.
"BGA technology is not just about packing more features; it's about maximizing efficiency and performance within constrained spaces."
In summary, this section aims to provide a foundational understanding of BGA packages—setting the stage for a more detailed investigation into their historical development, manufacturing processes, and applications in the modern electronic landscape.
Historical Overview
The historical context of Ball Grid Array (BGA) packages is critical to understanding their evolution and significance in modern electronics. It provides insight into the technological advancements and practical challenges that have influenced the design and implementation of BGA technology over time. By tracing the advancements from early development to contemporary uses, we can appreciate not only the engineering improvements but also the shifts in market demands and manufacturing capabilities.
Early Development
The initial steps towards the creation of BGA packages can be observed in the late 1980s. Previous packaging technologies like Dual In-line Package (DIP) and Surface Mount Device (SMD) had inherent limitations regarding pin density and thermal performance. BGA technology emerged as a solution, addressing critical shortcomings by relocating solder joints to the underside of the package.
The innovation allowed for a higher density of I/O connections without significantly increasing the board space. Early adopters focused on military and aerospace applications where reliability and performance were paramount. During this period, engineers and manufacturers experimented with various grid arrangements and sizes for the solder balls to enhance durability and connection integrity.
Evolution of BGA Technology
As the technology matured, the adoption of BGA packages expanded into consumer electronics and industrial applications throughout the 1990s and 2000s. This shift was primarily driven by the need for miniaturization in electronic devices, alongside increasing performance demands. The increased use of BGA packages aligned with the development of more sophisticated electronics, such as smartphones and laptops.
With each iteration, BGA technology has seen continuous improvements in materials and manufacturing processes. Advancements in solder ball formulations and reflow soldering techniques have heightened reliability and performance. Furthermore, industry standards such as IPC and JEDEC have emerged, ensuring levels of quality and compatibility in BGA production and performance.
By the 2010s, BGA packages became ubiquitous in various domains. Newer variants, such as Micro BGA and Fine Pitch BGA, addressed niche requirements, accommodating intricate designs for modern systems on chips. The continuous innovation in BGA technology reflects a broader trend of adaptation to meet the evolving needs of advanced electronics.
Key Characteristics of BGA Packages
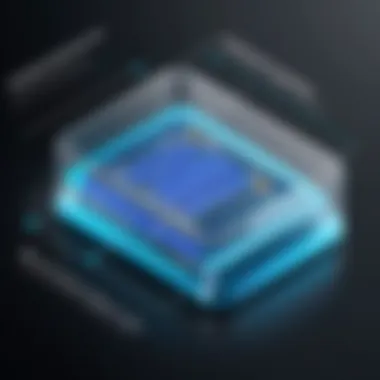
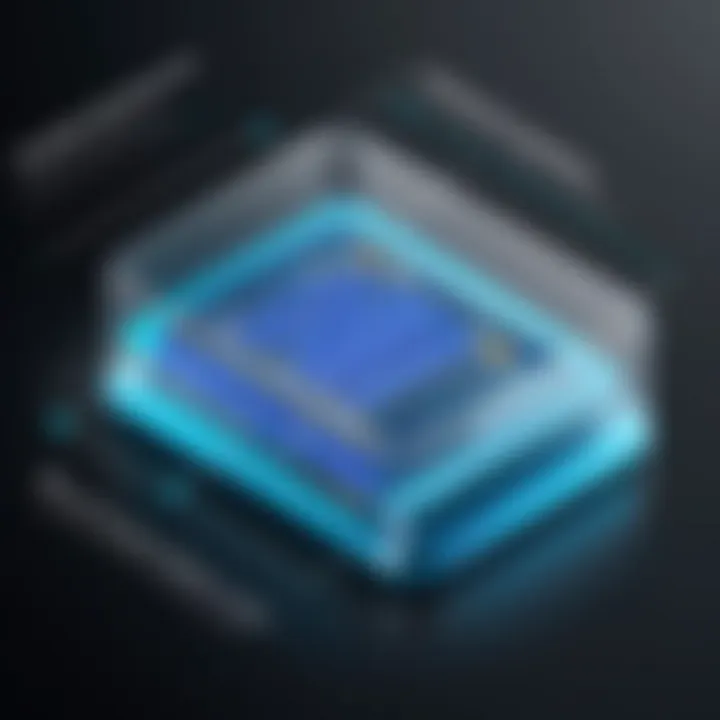
The key characteristics of BGA packages play a vital role in understanding their effectiveness and application in modern electronics. These features directly influence the performance, reliability, and overall efficiency of electronic devices. The intricacies involved in the design and functionality of BGA packages provide insights into why they have become a popular choice in the industry. This section dives into specific design attributes and electrical performance metrics that define BGA technology.
Design Features
Grid Arrangement of Solder Balls
The grid arrangement of solder balls is a critical aspect of BGA package design. This layout consists of multiple solder balls positioned in a grid format beneath the package. This architecture facilitates an increased pin density, meaning that a BGA can host more connections on a smaller footprint compared to other package types.
A key characteristic of this arrangement is its uniform distribution of electrical connections. When designed effectively, this setup leads to minimized inductance and capacitance, enhancing signal integrity during operation. This property makes grid arrangements a beneficial choice for various electronic applications.
However, the grid structure also comes with challenges. The precision required during manufacturing is higher compared to traditional packages. A misalignment can lead to significant issues, affecting overall performance, which must be taken into consideration.
Package Size and Form Factors
The package size and form factors of BGA packages are equally important. They come in various sizes, allowing designers the flexibility to choose one that fits their specific application needs. One notable feature is the ability to scale down component sizes without sacrificing performance. This characteristic is increasingly relevant in the current trend of miniaturization in electronics.
The popularity of compact BGA packages is mainly due to their efficient use of board space and ability to integrate more functionality. Additionally, smaller packages tend to have improved thermal performance. But, on the downside, selecting the wrong size can complicate thermal management and assembly processes.
Thermal Management
Thermal management is another crucial aspect of BGA packaging. With the rising demand for high-performance electronics, effective thermal management solutions need to be integrated into the design. The unique feature of BGA packages includes options for built-in thermal vias that help dissipate heat effectively.
This characteristic allows for improved heat distribution across the chip, which can enhance reliability and performance. Incorporating robust thermal management into BGA design can significantly improve operational longevity. However, failure to adequately address thermal challenges can lead to overheating and device failure, making it a double-edged sword in some applications.
Electrical Performance
Signal Integrity
Signal Integrity is a vital part of BGA packages that companies focus on during design. The arrangement of solder balls, along with the short and direct traces common in BGA packages, minimizes the interference and distortions in signals during transmission. This feature ensures that data retains its quality even in high-speed applications.
The commitment to maintain signal integrity makes BGA a popular choice for advanced electronics. However, achieving optimal signal integrity relies heavily on proper layout and planning; deviations may lead to substantial performance issues.
Impedance Control
Impedance control is integral to managing how signals transmit through connections. With BGA packages, designers ensure that the impedance levels are consistent. This characteristic supports high-frequency applications better than many alternatives because of its predictable electrical behavior.
The benefit here lies in reduced reflections and enhanced overall performance of the device. The downside, however, is that controlling impedance requires a deeper understanding of both the design and manufacturing processes. If not done correctly, performance might degrade.
Power Distribution
Power distribution in BGA packages is notably efficient due to their unique design. With multiple solder balls, the capability to distribute power to various sections of the semiconductor ensures balanced operation. This layout supports high current applications while minimizing the voltage drop across the power distribution network.
The great aspect of proper power management is improved system stability, which is vital for many high-performance or mission-critical applications. Yet, this design may require additional considerations such as how to prevent issues like hot spots or uneven power supply, emphasizing the need for thorough design strategies.
Understanding these characteristics is essential for professionals when deciding on BGA technologies.
Thus, the study of these key features at design and electrical performance levels provides a comprehensive understanding of BGA packages, highlighting their strengths and potential challenges as technologies evolve.
Advantages of Using BGA Packages
BGA packages carry several benefits that make them an attractive option for modern electronic designs. These advantages can significantly influence performance, reliability, and overall product design. Understanding these benefits is crucial for IT professionals and tech enthusiasts alike to leverage BGA technology effectively.
Higher Pin Density
One of the primary advantages of BGA packages is their higher pin density. With solder balls arranged in a grid underneath the package, BGA designs enable more connections within a smaller footprint compared to traditional packages like Surface Mount Devices (SMDs). This high pin density allows designers to fit more features into compact devices. The importance of higher pin density extends beyond mere connection count. It can improve the overall functionality of the circuit board, making it ideal for complex electronics, such as smartphones and advanced computing systems.
Improved Thermals
BGA technology also offers improved thermal management. BGA packages can efficiently dissipate heat due to their design, which integrates the thermal pad directly into the package. This is especially critical in high-performance applications, where components generate considerable heat. The thermal pads enhance heat spreading, reducing the risk of overheating and subsequent failures. By managing heat better, BGAs can extend the lifespan of electronic devices, which is a significant concern for manufacturers and end-users.
Soldering Benefits
The soldering process for BGA packages presents several benefits as well. First, the placement of BGA packages is more straightforward due to their ball grid arrangement. This design facilitates automatic assembly and can lead to a more reliable solder joint compared to traditional methods. Moreover, because the BGA’s solder balls elevate the package slightly off the board during reflow soldering, it minimizes the chances of defects. This quality allows for more repetitive and consistent results in high-volume manufacturing. Properly executed soldering of BGA devices can often lead to better electrical performance due to more reliable connections and less risk of solder joint failure.
BGAs represent a significant evolution in semiconductor packaging, effectively combining higher performance and design efficiency.
In summary, the advantages of using BGA packages notably enhance design capabilities in electronics. Higher pin density, improved thermal performance, and soldering efficiency make them favorable for modern applications.
Disadvantages of BGA Packages
In this section, we will discuss the disadvantages of using Ball Grid Array (BGA) packages. While BGA technology offers numerous benefits such as higher pin density and improved thermal management, it also presents certain challenges that need careful consideration. Understanding these disadvantages is crucial for IT professionals and tech enthusiasts who aim to select the most suitable packaging for their electronic components.
Inspection Challenges
One of the primary disadvantages of BGA packages is the challenges associated with inspection. Since the solder balls are located beneath the package, visual inspection becomes difficult. This positioning makes it hard to detect defects such as solder voids or bridging between the balls. Conventional inspection methods such as Automated Optical Inspection (AOI) are less effective here, as they cannot capture what happens underneath the package.
To overcome these hurdles, companies often rely on X-ray inspection systems. However, these systems come at a high cost, and not all facilities may have access to them. Additionally, the operator skill level plays a significant role in accurately interpreting the X-ray results. Misinterpretation can lead to undetected defects, which could affect the reliability of the assembly in the long run.
"Inspection challenges are one of the critical factors that contribute to the overall cost and complexity of using BGA packages."
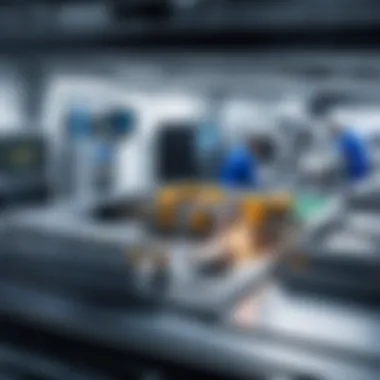
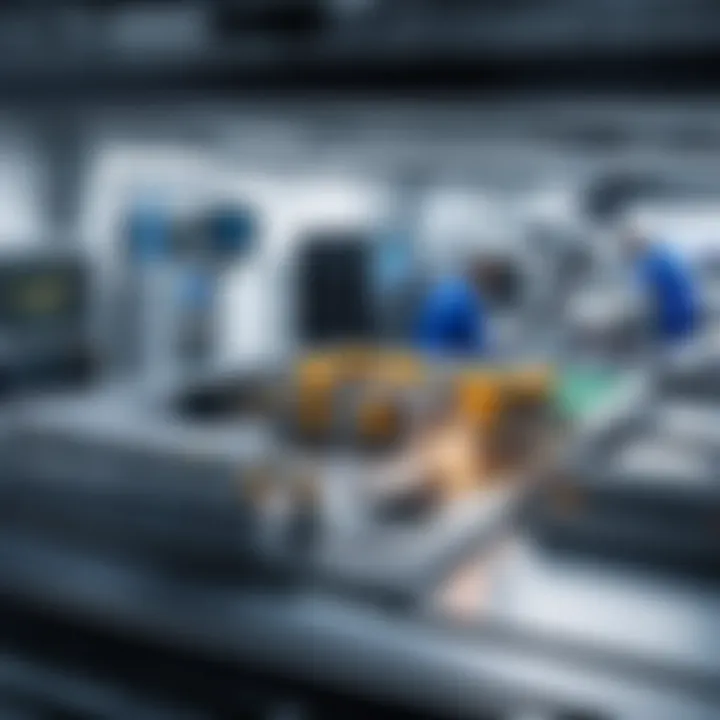
Rework Complications
Another significant disadvantage of BGA packages lies in the rework process. When a BGA component fails, reworking can be complex and time-consuming. The process requires precise alignment of the package with the pads on the circuit board, and any misalignment can lead to further defects.
Using traditional soldering methods may not suffice for BGA packages. Instead, specialized tools like solder reflow ovens or hot air rework stations are typically necessary. Even with these tools, the risk of damaging the PCB or the component during rework is higher compared to other package types, such as Surface Mount Devices (SMD).
Furthermore, excessive thermal exposure during rework can impact the integrity of nearby components. This includes potential delamination or damage to adjacent solder joints. As a result, the overall complexity and risks associated with reworking BGA packages can deter some manufacturers from using them, even if they offer substantial performance benefits.
In summary, while BGA packages present various advantages, the disadvantages related to inspection and rework pose significant considerations. Addressing these challenges is crucial for ensuring the reliability and longevity of the electronic products that use BGA technology.
Manufacturing Process of BGA Packages
The manufacturing process of Ball Grid Array (BGA) packages is essential to ensure reliability and performance in electronic devices. Every step in this process affects the final product’s quality, influencing how well it performs in various applications, whether in consumer electronics or industrial machinery. Understanding these processes aids technology professionals in comprehending potential pitfalls and highlights best practices for assembly and testing.
Solder Ball Placement Methods
Solder ball placement is a critical first step in the production of BGA packages. Precision in this stage directly impacts the performance of the finished product. There are several methods utilized in the industry for placing solder balls:
- Manual Placement: This is often used for low-volume production or prototypes. While it can provide accuracy, the consistency is variable and might lead to defects.
- Automated Placement: Using machines to accurately place solder balls has become the standard in high-volume manufacturing. Techniques such as pick-and-place machines ensure that solder balls are placed with high precision to avoid bridging and misalignment.
- Stencil Printing: This method involves applying solder paste onto specific areas of a print circuit board (PCB) before the balls are attached. It enhances the uniformity of solder balls and is often employed in contemporary manufacturing.
These methods are crucial in defining the electrical and thermal properties of BGA packages. Poor placement can lead to issues like short circuits, affecting the functionality of the device. Thus, assessing each method's appropriateness based on the specific application requirements is vital.
Reflow Soldering Techniques
Reflow soldering is the next step that solidifies solder connections. This process involves heating the printed circuit board to melt solder, creating strong electrical connections. The two primary techniques utilized in reflow soldering include:
- Convection Reflow: This is the most common method, utilizing hot air to heat the solder. It is effective but can have limitations in the control of temperature profiles, which is crucial for sensitive components.
- Infrared Reflow: This method employs infrared radiation to heat specific areas quickly. It can be more selective, which is essential for components sensitive to heat.
Both methods need careful calibration to avoid issues like overheating or cold solder joints. Conducting a thorough profile analysis ensures that solder joints are reliable while meeting strict thermal specifications.
Testing and Quality Assurance
Quality assurance is imperative throughout the BGA manufacturing process. Effective testing ensures that the BGA packages meet requirements for durability and performance. Key practices include:
- X-ray Inspection: This allows for the internal examination of solder joints without damaging the package. It helps in identifying defects such as voids, misaligned balls, or insufficient solder.
- Electrical Testing: Functionality tests can identify if the connections are performing as expected and allow early detection of issues.
- Thermal Cycle Testing: This tests the package's durability through repeated exposure to temperature extremes, simulating real-world conditions.
"The thorough testing of BGA packages not only ensures reliability but also significantly reduces potential failures in the field, benefiting manufacturers and end-users alike."
In summary, the manufacturing process of BGA packages is multifaceted, involving precise placement techniques, controlled soldering methods, and rigorous quality assurance. Mastering these elements leads to significant improvements in device performance and longevity, which is indispensable for today’s technological landscape.
Industry Standards for BGA Packaging
Understanding industry standards for Ball Grid Array (BGA) packaging is fundamental for ensuring the reliability, performance, and interoperability of electronic components. These standards are established by recognized institutions and are critical in guiding manufacturers and designers through the complexities of BGA packaging. They serve to help maintain quality control in production processes, making sure that the components meet industry expectations and can function effectively in various applications.
There are two principal organizations whose guidelines are particularly significant in this context: IPC and JEDEC. The following sections will delve into their specific standards and regulations, highlighting how they contribute to the overall integrity of BGA packages.
IPC Standards
IPC, originally known as the Institute for Interconnecting and Packaging Electronics Circuits, has developed a comprehensive suite of standards that address different aspects of electronic packaging. In terms of BGA packaging, IPC standards focus on performance criteria, soldering techniques, and testing procedures.
Some key IPC standards relevant to BGA are:
- IPC-A-610: Quality acceptability for electronic assemblies. This standard lays out criteria for the visual quality of BGA packages, ensuring that they meet certain aesthetic and operational benchmarks.
- IPC-7711/7721: Guidelines for repair and reclamation of electronic assemblies provide directions for rework and repair of BGA packages, emphasizing the importance of preserving functionality during the process.
- IPC-4590: This standard addresses the moisture sensitivity of BGAs, detailing how to properly store and handle these components to prevent damage due to humidity.
Adherence to IPC standards allows manufacturers to produce BGA packages that are reliable and efficient. Additionally, these benchmarks facilitate easier collaboration between different entities in the supply chain by ensuring a common understanding of quality expectations.
JEDEC Regulations
JEDEC is another crucial organization that sets standards for semiconductor engineering, and its regulations are essential for BGA packaging. JEDEC's standards focus primarily on helping manufacturers achieve consistency in the design, construction, and testing of semiconductor packages.
Key JEDEC standards related to BGA packages include:
- JESD22-B111: This standard addresses the testing methods for BGA solder ball reliability. It outlines necessary procedures to assess how well BGA packages can withstand thermal cycling, which is critical for ensuring longevity in various environments.
- JESD47: It provides guidelines for the qualification of semiconductor components, ensuring that BGA packages have a clear path to meeting life cycle and reliability criteria before they enter the market.
- JESD78: This standard outlines the guidelines for lead-free soldering processes which have become increasingly important with the industry's shift towards more environmentally friendly practices.
Compliance with JEDEC standards ensures that BGA packages can perform reliably in a range of conditions, which is vital for applications in demanding industries such as telecommunications and industrial equipment.
"Establishing and following industry standards not only enhances product quality but also reinforces consumer and stakeholder confidence in electronic technologies."
Applications of BGA Packages
Understanding the applications of BGA packages is crucial in today’s technological landscape. BGA packages are integral components in various industries due to their numerous benefits, such as compact design, enhanced performance, and reliability. As electronic devices continue to evolve, these packages find their way into diverse fields, impacting requirements and design protocols. The versatility of BGA packages serves as a foundation for innovation in product development.
Consumer Electronics
In the realm of consumer electronics, BGA packages have become ubiquitous. They are found in products such as smartphones, tablets, and laptops. The design features of BGA allow for a higher pin density, which is vital in shrinking the size of chips without sacrificing performance. This is particularly important as manufacturers strive to create more compact and user-friendly devices. Furthermore, BGA packages facilitate improved thermal management. Heat dissipation is a key consideration in portable electronics, where space is limited. The ability of BGA to manage heat efficiently prolongs the life of consumer devices, providing both longevity and reliability for end-users.
Industrial Equipment
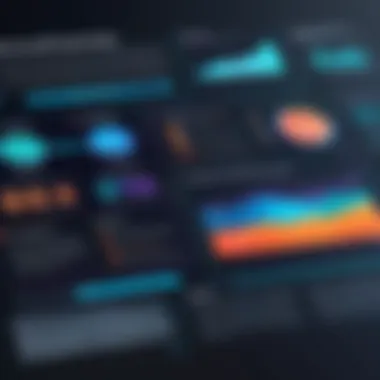
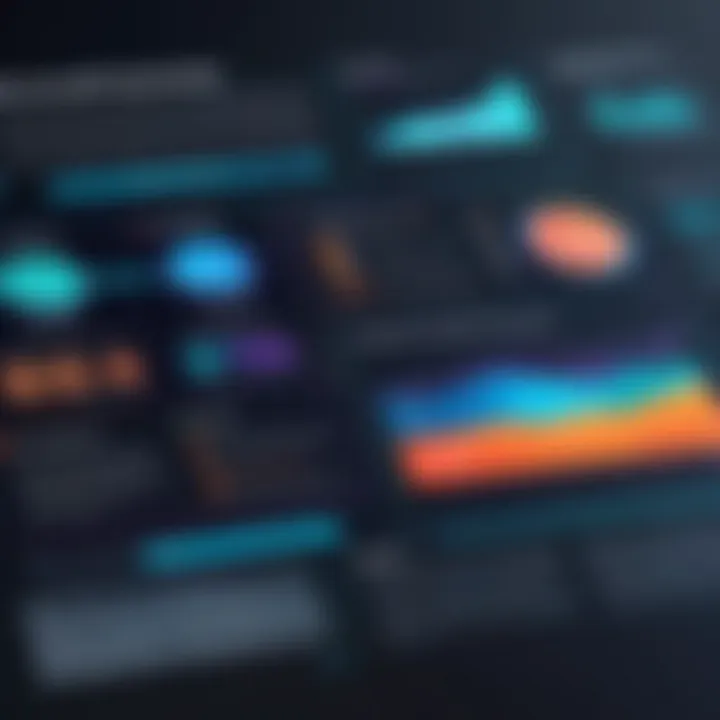
In industrial equipment, the robustness of BGA technology plays a significant role. These packages often endure harsh conditions, such as temperature fluctuations and heavy vibrations. BGA packages can withstand these challenges due to their sturdy nature and reliable solder connections. As industries incorporate advanced automation and smart technology, BGA packages enable the development of sophisticated machinery. Moreover, their electrical performance enhances signal integrity, which is vital for the operation of intricate industrial systems. Users benefit from the improved efficiency and reduced downtime, reinforcing the importance of BGA in this sector.
Telecommunications
In the field of telecommunications, BGA packages are key components in devices like routers, switches, and base stations. The need for high-speed communication requires components that are not only efficient but also reliable. BGA technology supports the demand for high-frequency operation, accommodating the rapid signal changes that are characteristic of modern communication systems. BGA also aids in minimizing signal loss through optimized impedance control. This quality becomes increasingly important as telecommunication infrastructure grows and evolves. The cohesive performance of BGA packages ensures that telecommunications providers can meet consumer demands without compromising on speed or quality.
The integration of BGA packages into consumer electronics, industrial equipment, and telecommunications showcases their versatility and technological importance.
Current Trends in BGA Packaging
Understanding current trends in BGA packaging is vital for professionals in the field. These trends impact design choices, manufacturing processes, and end-application effectiveness. Staying updated with these trends allows engineers and designers to leverage the latest developments for optimizing performance and reducing costs.
Miniaturization
Miniaturization has become a defining trend in BGA packaging. As electronic devices become smaller and more complex, the demand for compact packaging solutions increases. BGA technology supports this by enabling higher pin densities without the need for significant increases in footprint area.
Manufacturers are developing BGA packages with smaller pitch sizes. This allows for more solder balls to be integrated into the same surface area. Consequently, it enables the design of smaller circuits with enhanced capabilities. Notably, devices for wearables and mobile electronics see the most significant benefits from this trend.
"Miniaturization in BGA packages not only addresses space constraints but also improves overall product efficiencies."
Additionally, advancements in manufacturing techniques, such as precision solder ball placement and improved surface finishes, contribute to successful miniaturization efforts. The effective heat dissipation of compact BGA designs is critical, and innovations in thermal management solutions play an essential role.
Advancements in Materials
The landscape of BGA packaging is also influenced by advancements in materials. Improved materials enhance the reliability and performance of BGA packages in various environments. For instance, new types of substrates are developed using high-density interconnects, which facilitate better signal integrity and thermal dissipation.
Some of the notable material advancements include:
- Low-Dielectric Constant Materials: These materials reduce signal loss and improve the speed of signal transmission. As high-frequency operations become commonplace, this property is essential.
- Thermal Interface Materials: Enhanced thermal interface materials provide better thermal conductivity, enabling BGA packages to manage heat more efficiently. This is particularly crucial for high-performance computing applications.
- Flexible Substrates: These materials allow for the integration of BGA packages in flexible or curved electronic devices. This adaptability is becoming increasingly important as industries explore innovative product designs.
The choice of materials not only affects performance but also influences the longevity of the components. As reliability demands grow, material selection will continue to be a critical factor in future BGA packaging strategies. In summary, both miniaturization and advancements in materials are reshaping the BGA packaging industry, offering exciting opportunities and challenges for technology professionals.
Future Developments in BGA Technology
The exploration of future developments in BGA technology is essential in understanding how this packaging approach can adapt and evolve in response to the continuous demands of the electronics industry. As technology advances, the need for smaller, more efficient components increases. BGA packages, by their very nature, are well-suited to meet these challenges. They provide a reliable method of connectivity while allowing for enhanced performance, making them a focal point for future innovations.
Emerging Techniques
Emerging techniques in BGA technology focus on optimizing both performance and manufacturability. Many of these methods involve new materials and processes enhancing thermal, electrical, and mechanical properties. Some notable techniques include:
- Micro-BGA and Fine-Pitch BGA: These variations significantly reduce the size of the solder balls and pitch, facilitating a much higher density of pins. The result is a smaller footprint that meets the needs of modern compact devices.
- Advanced Reflow Techniques: Innovating in reflow methods ensures that solder joins form more uniformly, leading to better reliability. Techniques like vapor phase reflow or laser reflow processes are settings to scrutinize.
- 3D Packaging Integration: Implementing three-dimensional stacking of BGA packages can revolutionize the design of multi-chip modules. This technique utilizes vertical space effectively, providing greater efficiency without increasing overall size.
The significance of these techniques lies in their potential to enhance both the performance of devices and the ease of manufacturing, suggesting a shift in how electronic products are designed and assembled.
Market Projections
As the BGA market continues to evolve, key projections provide insight into its future trajectory. The trends indicate that demand will expand primarily in sectors such as consumer electronics, automotive, and telecommunications. Relevant projections include:
- Growth in Consumer Electronics: There is an expected surge in BGA packaging use in smartphones, laptops, and wearables due to increased functionality requiring higher pin density and improved thermal management.
- Automotive Sector's Influence: With the rise of electric vehicles and complex electronic systems, BGA packages are anticipated to play a vital role in ensuring reliability and performance under diverse conditions.
- Telecommunications Expansion: The 5G rollout demands heightened performance in devices. BGA packaging remains a critical enabler for high-speed signal processing and improved thermal management.
Emerging trends in BGA technology reflect a continuous commitment to innovation in electronic assembly methods.
As we look forward, it's evident that the advancements in BGA packages will significantly contribute to the development of future electronic devices, promoting both efficiency and reliability.
Selecting the Right BGA Package
The selection of the appropriate Ball Grid Array (BGA) package is paramount for ensuring optimal performance in electronic devices. The choice significantly influences both the technical aspects of the circuit design and the overall cost-effectiveness of the production process. A well-selected BGA package can lead to enhanced signal integrity, improved thermal management, and greater reliability of the end product. Conversely, an ill-suited package may result in operational inefficiencies and increased challenges during the manufacturing process.
Criteria for Choice
When evaluating various BGA packages, several criteria should be taken into account:
- Application Requirements: Consider the specific needs of the application, which can dictate the size, shape, and pin configuration of the BGA.
- Thermal Performance: Evaluate how the BGA package meshes with the thermal management strategies in place. High power applications may necessitate packages with better heat dissipation features.
- Electrical Performance: Concentrate on the signal integrity and impedance control. The characteristics of the BGA must meet or exceed the standards required for maintaining optimal performance and preventing signal degradation.
- Cost Factors: Assess the costs associated, not just in terms of the purchasing price of the BGA package itself, but also the implications for assembly and rework.
- Manufacturer Recommendations: Pay attention to recommendations from manufacturers regarding the compatibility of BGA packages with different PCBs and associated components.
Best Practices for Implementation
To effectively implement the chosen BGA package, consider the following best practices:
- Thorough Design Verification: Perform comprehensive simulations of the PCB design to validate that the selected BGA package fulfills all operational parameters in real-world scenarios.
- Controlled Temperature Environment: Ensure that assembly processes are conducted in a controlled thermal setting to maintain solder integrity. Proper reflow techniques must be applied.
- Test Before Production: Implement rigorous testing phases prior to full-scale production. This reduces the likelihood of defects and unwelcome surprises in later stages.
- Document the Process: Maintain clear and detailed documentation of the manufacturing process, assembly guidelines, and troubleshooting steps to facilitate easier future revisions and improvements.
In summary, selecting the right BGA package significantly impacts electronic device performance and reliability. Understanding the criteria for choice and adhering to best practices for implementation is essential for successful and efficient production.
Finale
The conclusion of this article is not just a summary; it is a critical element that ties together all the themes and insights presented about BGA packages. A succinct conclusion encapsulates the comprehensive nature of Ball Grid Array technology, affirming its significance in modern electronics.
In emphasizing the importance of understanding BGA packages, one identifies multiple layers of benefits that contribute to effective decision-making for professionals in technology. First, grasping the advantages of BGA structures allows engineers and designers to leverage their high pin density and improved thermal performance. This aids in achieving superior device reliability and efficiency, especially in compact designs.
However, acknowledging the drawbacks, such as inspection challenges and rework complications, further enriches one's perspective. It spurs conversations and considerations around advances in manufacturing and inspection technologies that can mitigate these issues. Thus, the awareness of both sides fosters a well-rounded discourse among IT professionals and tech enthusiasts.
Furthermore, the conclusion paves the way for readers to reflect on the criteria for selecting the right BGA package. It underscores the necessity for informed choices and the best practices that promote successful implementation. This aspect is particularly vital, as it potentially affects the overall cost, performance, and longevity of electronic products.
"Understanding BGA technology is not merely academic; it is pivotal for fostering innovation in electronics design and development."
As the exploration into current trends and future projections unfolds, the conclusion reiterates the dynamism within BGA packaging and its potential implications for future innovations. This segment encourages ongoing engagement with the subject, promoting continuous learning and adaptation in a rapidly evolving field. In summary, an effective conclusion not only encapsulates the presented information but also serves as a catalyst for further exploration and discussion within the electronics community.